What is Dry for Wheat: Understanding the Essentials
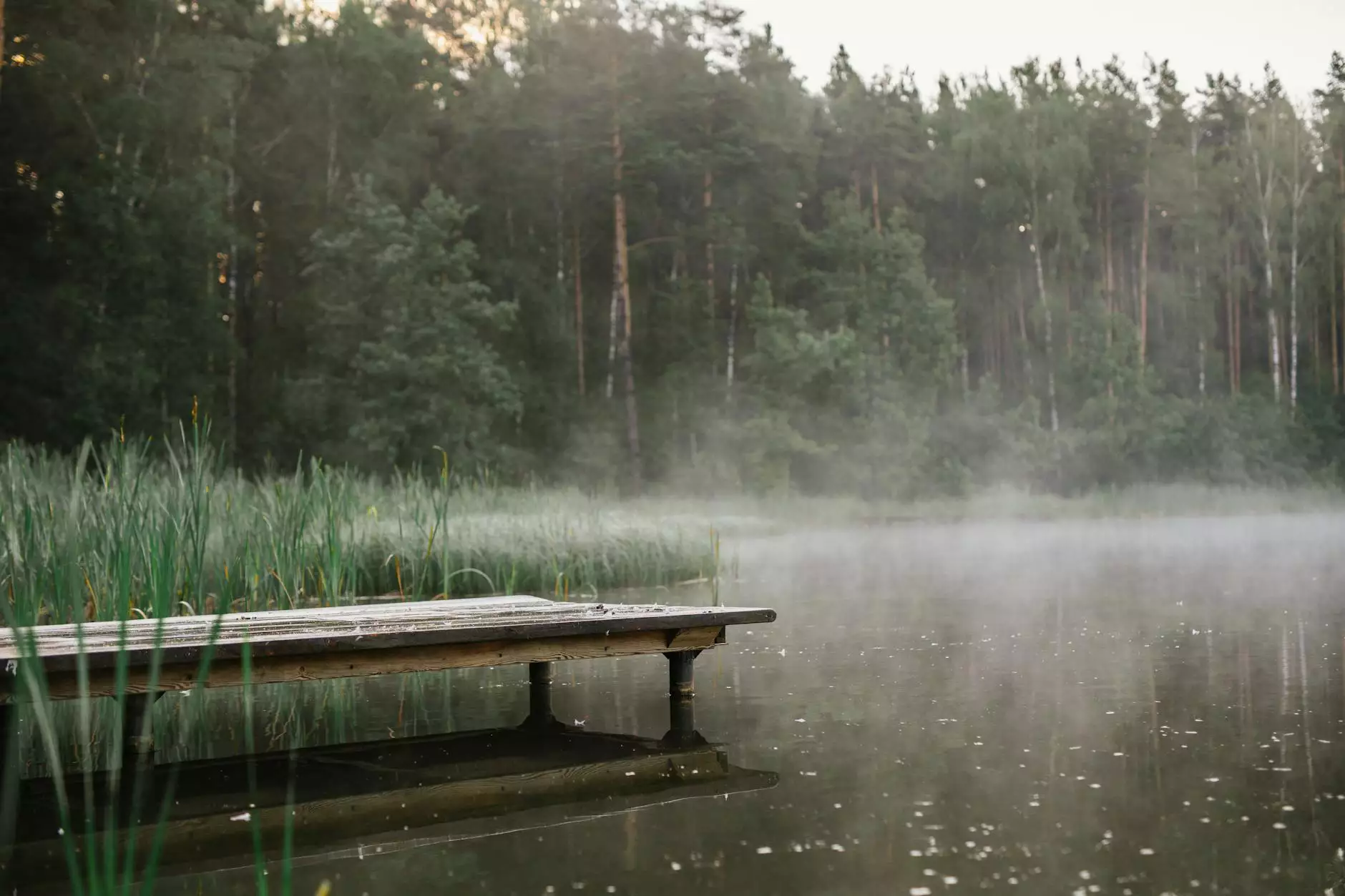
Wheat is one of the staple grains that serve as a cornerstone for food production globally. Understanding the concept of drying wheat is crucial for farmers aiming to maximize their yield and maintain the quality of their produce. In this comprehensive guide, we will explore various aspects of wheat drying, including best practices, equipment used, and the implications it has on farming.
The Significance of Drying Wheat
Drying wheat is a critical step in the harvesting process. It's essential to reduce moisture levels in the grain to prevent spoilage, mold growth, and grain degradation. High moisture content can lead to various issues during storage, which can diminish the grain's viability and market value.
1. Understanding Moisture Content
Moisture content is typically expressed as a percentage and is crucial for determining when to harvest wheat. Generally, wheat needs to be at a moisture level of 13-14% before it is stored. This makes understanding what is dry for wheat imperative for anyone in the farming business.
- Optimal Moisture Levels: Keeping moisture levels within optimum ranges helps enhance the grain's longevity.
- Preventing Spoilage: Drying reduces the risk of spoilage and ensures the wheat remains edible and marketable.
- Enhancing Quality: Properly dried wheat retains its nutritional value, ensuring it is suitable for consumption and processing.
2. The Drying Process
The drying process involves various methods and technologies tailored to the type of wheat, environmental conditions, and available resources. Understanding these processes can significantly affect the health and profitability of wheat farming.
2.1 Natural Air Drying
One of the simplest methods is natural air drying, which utilizes sunlight and wind to lower moisture content. Farmers spread the harvested wheat in thin layers on drying pads or tarps. However, this method is highly dependent on weather conditions and can take several days to achieve desired moisture levels.
2.2 Mechanical Drying
Mechanical drying is a faster and more reliable method. Grain dryers use heat to reduce moisture content effectively. Types of mechanical drying systems include:
- Batch Dryers: Ideal for smaller volumes, these dryers allow farmers to load and unload batches of grain using hot air.
- Continuous Flow Dryers: Designed for larger operations, these systems continuously move wheat through a drying chamber.
- Fluidized Bed Dryers: These dryers offer an advanced method by suspending grains in hot air, ensuring uniform drying.
Choosing the Right Equipment
The choice of equipment for drying wheat significantly influences efficiency and profitability. Here are some options available for farmers:
3.1 Grain Bins and Silos
Investing in grain bins or silos equipped with aeration systems can help maintain proper moisture levels during storage. These systems draw in air to keep the grain dry and reduce spoilage risks.
3.2 Humidity Control Devices
Humidity control devices are essential in monitoring moisture levels across storage locations. These tools ensure farmers can respond quickly to changes in conditions and take appropriate actions to preserve grain quality.
3.3 Automated Drying Systems
Advanced automated systems can significantly improve efficiency. These include humidity sensors, thermostat controls, and programmable machines that optimize drying times based on real-time data.
Impact of Weather on Wheat Drying
The weather plays a crucial role in the efficiency of the drying process. Factors to consider include:
4.1 Humidity Levels
High humidity can slow down the drying process, making it crucial to monitor weather conditions during the harvest. If humidity levels are high, it’s advisable to use mechanical drying methods to ensure timely drying.
4.2 Temperature Variations
Temperature is another significant factor. Warmer temperatures enhance the drying process, while cooler temperatures can prolong equipment use and increase costs. Farmers should strive to harvest during warmer periods if possible.
Common Challenges in Drying Wheat
Drying wheat is not without challenges. Here are common problems and their solutions:
5.1 Overdrying
Overdrying can lead to grain breakage and loss of vital nutrients. Farmers should constantly monitor moisture levels and use moisture meters for accuracy.
5.2 Inconsistent Drying
Inconsistency can arise from uneven airflow in drying systems. Regular maintenance of grain dryers and proper loading techniques can promote uniform moisture levels across the batch.
5.3 Cost Management
Operating drying equipment can be expensive. Efficient management practices, such as scheduling drying during low energy tariff periods, can help mitigate costs.
The Economic Benefits of Proper Drying Techniques
Implementing effective drying processes can yield significant economic benefits for farmers:
6.1 Better Grain Quality
High-quality wheat can demand better prices in the market. Thus, investing in effective drying solutions is crucial for ensuring top-notch grain quality.
6.2 Reduced Waste
Proper drying reduces waste caused by spoilage, thus improving overall yield and profitability.
6.3 Long-Term Storage
Effective drying allows farmers to store their wheat for extended periods, enabling them to take advantage of favorable market conditions.
6.4 Increased Market Competitiveness
Farmers who can deliver consistently high-quality, well-dried wheat position themselves favorably in the competitive agricultural market.
Conclusion: Embracing Technology and Best Practices
As the agricultural landscape continues to evolve, understanding what is dry for wheat becomes increasingly important. Farmers who invest in quality drying practices and equipment will not only contribute to the sustainability of their operations but also enhance their competitiveness in the market.
Remember, effective wheat drying is not merely a process; it's a critical part of the agricultural value chain that influences everything from grain quality to economic viability. To learn more about enhancing your farming practices, explore our offerings at tsgcinc.com.