Die Casting Mold Supplier: Elevating Your Manufacturing Insights
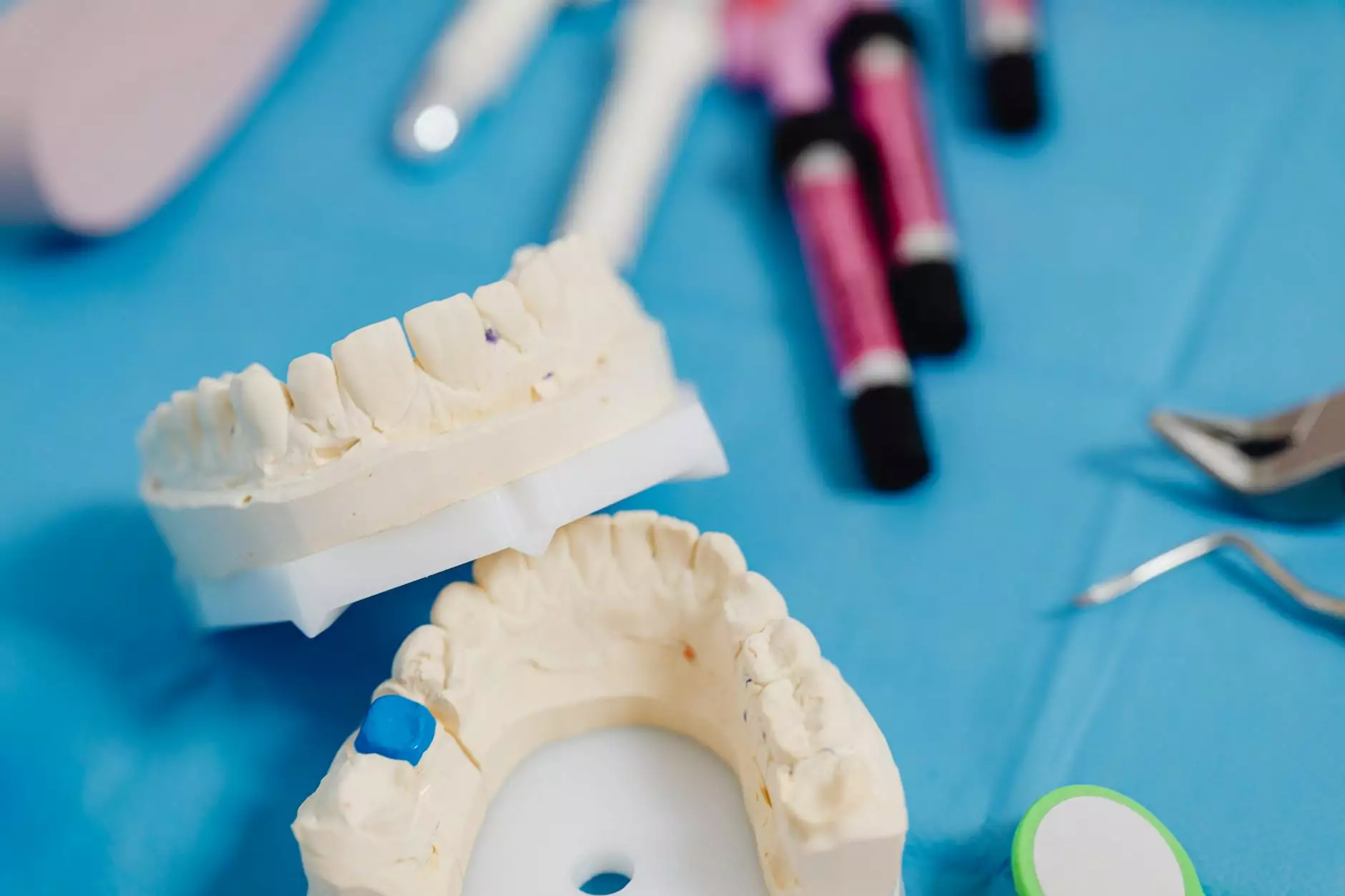
In the evolving world of manufacturing, the role of a die casting mold supplier is pivotal. From automotive parts to intricate electronic components, die casting has become a critical process for various industries. This article dives deep into what die casting is, the importance of selecting a superior mold supplier, and how these choices can impact your overall productivity and quality.
Understanding Die Casting
Die casting is a versatile and efficient manufacturing process used for producing complex metal parts. It involves forcing molten metal under high pressure into a mold cavity. The process has numerous advantages that make it a preferred manufacturing method:
- Precision: Die casting allows for high precision in manufacturing, creating parts with tight tolerances.
- Complexity: It enables the production of complex geometries that would be difficult or impossible to achieve with other methods.
- Efficiency: Once the mold is created, parts can be produced rapidly, which increases throughput and lowers production costs.
- Material Variety: A range of materials can be used in the die casting process, including zinc, aluminum, and magnesium, each offering unique advantages.
The Importance of a Quality Die Casting Mold Supplier
Choosing the right die casting mold supplier can significantly influence the overall success of your manufacturing operations. Here are a few reasons why:
1. Quality Assurance
A reputable supplier will ensure that molds are made from high-quality materials and with precise engineering techniques. This quality assurance leads to:
- Reduced Defects: High-quality molds will reduce the likelihood of defects in the finished products.
- Longevity: Durable molds lead to longer lifespans, which translates to lower costs per part.
2. Technological Expertise
In the era of fast-paced technological advancement, it's important to select a supplier that stays updated with the latest trends and technologies in die casting. Knowledge in:
- 3D Printing: Some modern suppliers use 3D printing to create prototypes quickly for testing purposes.
- Advanced Materials: Understanding the characteristics of various modern materials can improve the overall outcome of your products.
3. Custom Solutions
Every business has unique needs. A quality die casting mold supplier will work with you to develop custom solutions tailored to your specific requirements. This includes:
- Prototyping Services: Rapid prototyping can help in testing and verifying designs before mass production.
- Design Modifications: Sometimes your design may need adjustments for optimal manufacturability. A good supplier will offer design assistance.
4. Cost Efficiency
While it may seem that choosing a low-cost supplier saves money, partnering with a professional die casting mold supplier can lead to long-term savings. Cost efficiency arises from:
- Reduced Scrap Rates: Quality molds lead to lower scrap rates and better material utilization.
- Improved Cycle Times: Efficient manufacturing processes produced by a skilled supplier can help to reduce cycle times.
Key Considerations When Choosing a Die Casting Mold Supplier
With numerous suppliers available, it can be challenging to make a decision. Consider the following factors to help guide your choice:
1. Experience and Reputation
Investigate the experience of potential suppliers in the industry. Look for:
- Client Testimonials: Positive feedback from previous customers speaks volumes about their reliability.
- Portfolio of Work: Reviewing their past projects can show their capabilities and specializations.
2. Customer Service
Strong communication and customer service are vital. A supplier should be responsive and willing to assist you throughout the production process. Consider:
- Responsiveness: How quickly do they answer inquiries and resolve issues?
- Support Services: Do they offer technical assistance when needed?
3. Technological Capabilities
Assess the technological capabilities of the supplier. A modern supplier should have the latest equipment and software for:
- Mold Design and Simulation: Advanced software can simulate the casting process before actual production begins.
- Quality Control Technologies: Automated inspection systems can ensure that every part meets specifications.
4. Location
The geographical location of your supplier can impact lead times, shipping costs, and communication. A nearby supplier often means:
- Quicker Turnarounds: Shorter distances lead to faster production times and easier transportation.
- On-site Visits: Being able to visit the supplier’s facility can help build a stronger business relationship.
DeepMould.net: Your Premier Die Casting Mold Supplier
If you are looking for a trusted partner, DeepMould.net stands out as a premier die casting mold supplier that emphasizes quality, reliability, and technological advancement. With years of experience in the industry, we offer:
Comprehensive Services
From prototype development to full-scale production, we support your needs at every phase of the manufacturing process:
- Custom Mold Design: Tailored solutions to satisfy your specific requirements.
- Rapid Prototyping: Fast and efficient prototyping services to accelerate your time-to-market.
Commitment to Quality
At DeepMould.net, we take quality seriously. Our strict quality control processes ensure:
- Precision Engineering: Every mold is built to precise specifications to minimize defects.
- Material Selection: We use only high-grade materials that meet industry standards.
Client-Centric Approach
We believe in building strong relationships with our clients. Our customer service team is always ready to assist, ensuring smooth communication and effective problem-solving.
Conclusion
Choosing the right die casting mold supplier is crucial for any business looking to enhance its manufacturing capabilities. By focusing on quality, technological innovation, and customer support, you can ensure that your production processes are efficient and reliable. With DeepMould.net as your partner, you can access the expertise and services necessary to achieve your manufacturing goals.